When it comes to plastic injection molding, there are various components and machinery involved in the process. While the molds and machines often take the spotlight, there's one crucial component that deserves recognition for its indispensable role in the process – the screw barrel. Serving as the heart and soul of plastic injection molding machines, screw barrels play a vital role in ensuring the success and efficiency of the entire manufacturing process. Let's delve into the world of screw barrels and discover why they are the unsung heroes of plastic injection molding.
Injection molding is a widely used manufacturing technique for producing plastic parts and products. It involves injecting molten plastic material into a mold cavity, where it cools and solidifies to take the desired shape. The heart of the injection molding machine is the screw barrel assembly, which comprises two key components: the screw and the barrel.
The screw barrel assembly works in a cyclic manner to facilitate the injection molding process. The screw, driven by a motor, rotates within the barrel, melting the plastic material as it moves forward. The molten plastic is then forced through the nozzle and injected into the mold cavity. Once the plastic solidifies, the screw retreats, and the cycle repeats.
One of the primary functions of the screw barrel is to melt and mix the plastic material efficiently. The screw's design, including its flight depth, channel width, and compression ratio, plays a crucial role in achieving proper melting and mixing of the plastic. By controlling the temperature, pressure, and speed of the screw rotation, manufacturers can ensure that the plastic material reaches the ideal consistency for injection.
Furthermore, screw barrels also play a crucial role in maintaining consistent temperature control throughout the process. The barrel is equipped with heating and cooling elements that help regulate the temperature of the molten plastic. Precise temperature control is essential to prevent defects in the molded parts and ensure consistent quality across production runs.
The durability and quality of screw barrels are paramount to the success of the injection molding process. They are subjected to high temperatures, pressures, and abrasive plastic materials, making them prone to wear and tear. To combat this, screw barrels are often made from high-quality materials such as nitrided steel, bimetallic alloys, or ceramic coatings. These materials enhance their resistance to corrosion, abrasion, and thermal degradation, prolonging their lifespan and ensuring reliable performance.
Maintenance and proper care of screw barrels are crucial for their longevity and performance. Regular cleaning, inspection, and preventive maintenance can help identify and address any potential issues before they escalate. As screw barrels are intricate components, manufacturers should work closely with experts who specialize in their repair and maintenance, ensuring optimal performance and minimizing downtime.
In recent years, advancements in technology have further improved the performance and efficiency of screw barrels. Innovative designs, such as barrier screws and mixing screws, have enhanced the melting and mixing capabilities of the screw barrel assembly. Additionally, the use of advanced coatings and surface treatments has improved wear resistance, reducing the need for frequent replacements and minimizing production disruptions.
While screw barrels may not grab the headlines, their significance in plastic injection molding cannot be overstated. They are the unsung heroes that ensure consistent quality, high production efficiency, and reliable performance in the manufacturing of countless plastic products we encounter every day. Without these robust and resilient components, the injection molding industry would struggle to meet the demands of various sectors, ranging from automotive and electronics to consumer goods and medical devices.
So, the next time you come across a plastic product, take a moment to appreciate the unsung heroes behind its creation. Screw barrels may not be glamorous, but they are undoubtedly the backbone of plastic injection molding, enabling the production of intricate and high-quality plastic parts that shape our modern world.
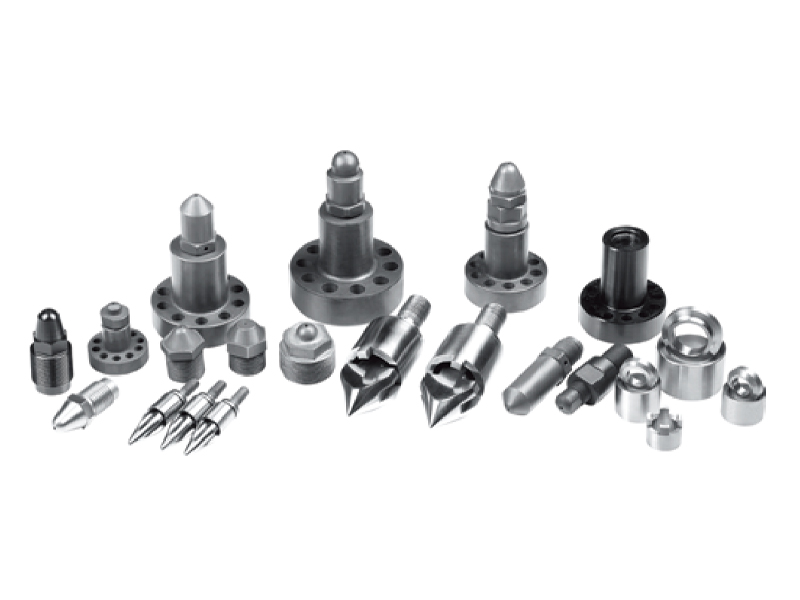
The products of INTAI in all series have perfectly integrated its experience for over 20 years and the technical development achievements in the 21st century. The products of INTAI widely cover nearly all fields in plastic processing and meet the diverse demands of all kinds of manufacturers on the manufacturing of general plastics products and precision products in batches.