In the realm of cable manufacturing, innovation plays a vital role in meeting the ever-evolving demands of the industry. As technology continues to advance, there is a growing need for high-quality cables that can deliver superior performance in various applications. To achieve this, extrusion processes must be enhanced, and one critical component at the heart of cable extrusion is the screw barrel. In recent years, a cutting-edge screw barrel design has emerged, revolutionizing cable extrusion and unlocking new possibilities for advanced cable production.
The screw barrel, commonly used in plastic extrusion processes, has found its niche in cable manufacturing. It is a combination of a rotating screw and a stationary barrel, working together to melt, mix, and convey the plastic material uniformly. This molten plastic is then forced through a die, resulting in a precisely shaped cable.
The traditional screw barrel design has served the industry well, but the demands for higher performance cables have necessitated a breakthrough in the extrusion process. The cutting-edge screw barrel design addresses this need by introducing innovative features that enhance productivity, efficiency, and cable quality.
One key feature of the advanced screw barrel design is the incorporation of modular elements. These modules consist of individual segments with specialized functions, such as melting, mixing, and conveying. Unlike the traditional design, these modular elements can be easily replaced or rearranged, allowing for quick customization and adaptability to different cable specifications. This flexibility significantly reduces downtime during changeovers, enabling manufacturers to respond swiftly to market demands.
Another notable improvement in the cutting-edge screw barrel design is the integration of advanced materials and surface treatments. High-performance alloys and coatings are applied to critical areas of the screw barrel, enhancing wear resistance and corrosion protection. This extends the lifespan of the screw barrel and ensures consistent performance over an extended period. Moreover, the improved surface finish reduces friction, leading to higher extrusion speeds and reduced energy consumption.
Furthermore, the cutting-edge screw barrel design incorporates advanced heating and cooling systems. Precise temperature control throughout the extrusion process is crucial for maintaining material consistency and achieving optimal cable properties. The innovative design integrates efficient heating elements and cooling channels, enabling accurate temperature regulation, even for high-speed extrusion. This temperature control capability enhances cable quality, minimizes defects, and reduces production waste.
The implementation of state-of-the-art sensor technology is another hallmark of the advanced screw barrel design. Sensors strategically placed along the screw barrel monitor various parameters, including temperature, pressure, and material flow. Real-time data from these sensors can be analyzed using advanced algorithms, providing valuable insights into the extrusion process. Manufacturers can leverage this information to optimize process parameters, improve cable quality, and troubleshoot issues promptly.
The cutting-edge screw barrel design is a result of collaboration between cable manufacturers, material scientists, and equipment suppliers. Through their collective expertise and dedication, they have unlocked a new era of innovation in cable extrusion. This breakthrough enables the production of advanced cables with enhanced electrical properties, mechanical strength, and resistance to environmental factors.
The impact of the cutting-edge screw barrel design extends beyond cable performance. Manufacturers also benefit from increased productivity, reduced downtime, and improved operational efficiency. The adaptability and modularity of the screw barrel design empower them to explore new cable designs and enter new markets swiftly.
In conclusion, the cutting-edge screw barrel design represents a significant leap forward in cable extrusion technology. Its modular elements, advanced materials, precise temperature control, and sensor integration revolutionize the extrusion process. This innovation unlocks new possibilities for advanced cable production, meeting the growing demands of various industries. As the cable manufacturing landscape continues to evolve, the cutting-edge screw barrel design paves the way for continued innovation and excellence in cable extrusion.
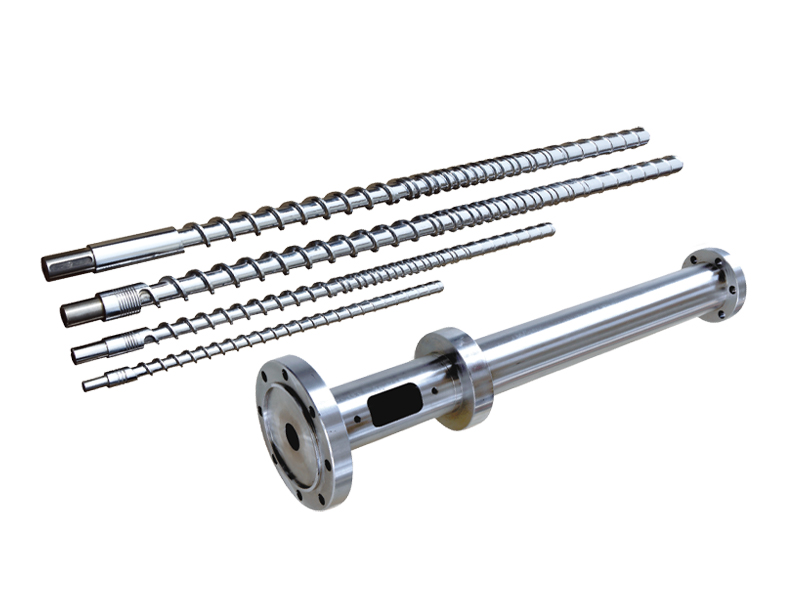
Screw Barrel For Extrusion Of Cable
Cable made of HDPE, PVC, LDPE, XLPE, LSHF, TPU, LSOH, LSLH, Fluoroplastic teflon (high-temperature) and Silicone rubber insulation material
Widely used for electronic wire, special cable, power line, building wire, insulating sheath, telephone wire, military product, audio line, network cable, power cable, blank pipe, copper cable lock rope and automobile cable, etc.