Parallel twin screw barrels have become an essential tool in the plastic extrusion industry. The technology has been around for decades, but the recent advancements have made it even more crucial to improving extrusion performance.Parallel twin screw barrels are an advancement over single-screw extruders. They have two screws that rotate in opposite directions inside a barrel, allowing for better mixing and melting of the plastic material. The parallel arrangement of the screws provides a high degree of flexibility in terms of processing a wide range of materials, including highly viscous and complex ones.
One of the significant benefits of parallel twin screw barrels is their ability to process a larger range of materials than single-screw extruders. With the ability to use different screw configurations, you can tailor the process to suit the specific material you are processing. This flexibility is essential when processing highly viscous materials such as PVC, which can be challenging to process with single-screw extruders.
Another significant advantage of parallel twin screw barrels is their ability to achieve higher output rates than single-screw extruders. The twin screws can process more material at a faster rate, which translates into higher production rates. Additionally, the parallel configuration of the screws allows for better mixing of the material, which can lead to a higher-quality end product.
Parallel twin screw barrels also have a shorter residence time than single-screw extruders. This means that the material spends less time in the extruder, reducing the chances of thermal degradation. Thermal degradation can result in changes in the material's properties, such as a decrease in molecular weight or an increase in viscosity. The shorter residence time of parallel twin screw barrels can help prevent these issues, resulting in a higher-quality end product.
The ability to use parallel twin screw barrels in tandem with downstream equipment also provides significant benefits. For instance, you can use a twin screw extruder to produce a masterbatch, which can then be fed into a single-screw extruder for further processing. This can help you achieve a better dispersion of pigments and other additives, resulting in a higher-quality product.
In conclusion, parallel twin screw barrels offer significant benefits to the plastic extrusion industry. Their ability to process a wider range of materials, achieve higher output rates, and reduce thermal degradation make them an essential tool for improving extrusion performance. With the ability to tailor the process to suit the specific material you are processing, parallel twin screw barrels can help you achieve higher-quality end products.
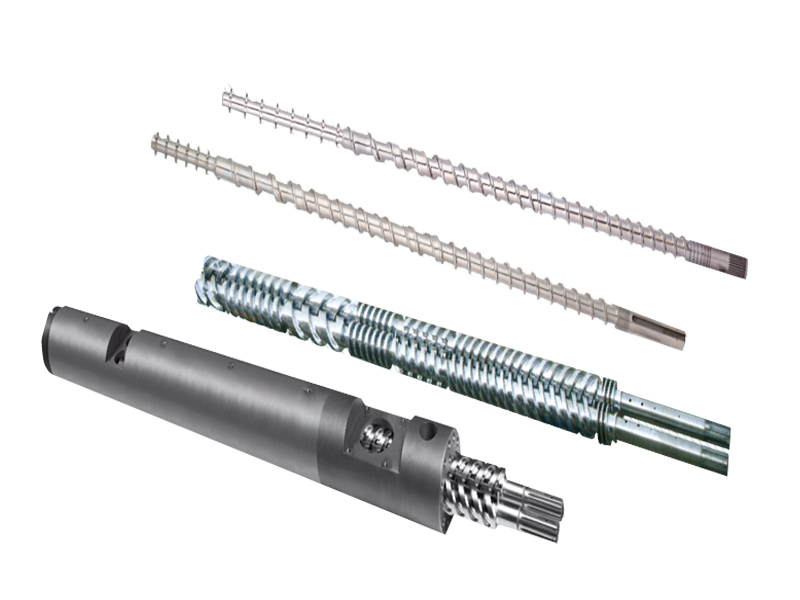
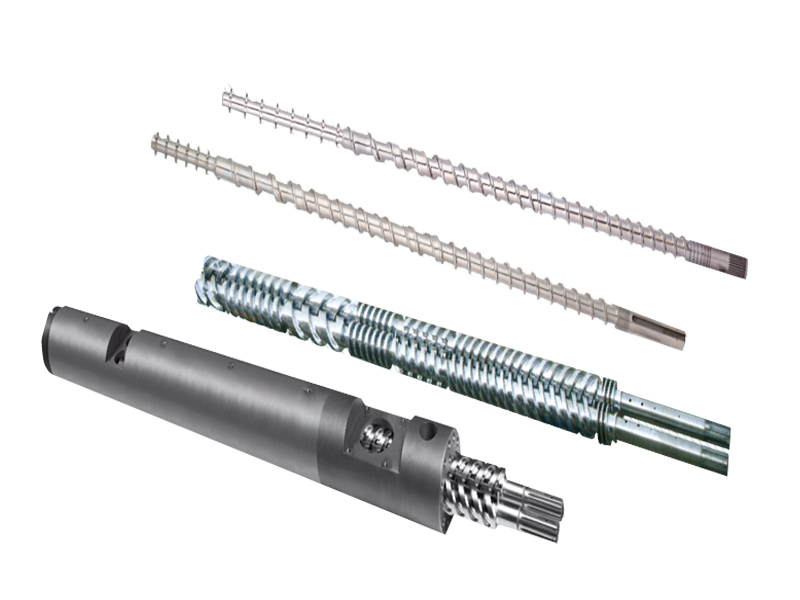
Zhoushan Intai Screw Manufacture Co.,Ltd. is a leading high-quality Screw barrel for extrusion of tubular products manufacturer. By virtue of over 20 years of professional experience, INTAI has been growing at a steady pace and has been always committed to creating a world top provider of Screw barrel for extrusion of tubular products. It owns a series of unique functions for R&D, design, production and aftersales which enable the products to be distinguished from others.
We only use first-class and check every production procedure to ensure precise production of every size. A final complete inspection will be performed before dispatch.