Bimetallic screw barrels are critical components in many plastic processing industries. They are used in the manufacture of a wide range of products, including plastic bags, bottles, and containers, among others. Understanding the basics of bimetallic screw barrels is crucial for anyone involved in plastic processing. We will provide a comprehensive guide to bimetallic screw barrels, covering everything you need to know.
What are bimetallic screw barrels?
A bimetallic screw barrel is a type of barrel that is made up of two different alloys or metals. It is designed to improve the performance and durability of extrusion and injection molding machines. The outer layer is typically made of a wear-resistant material, such as nitrided steel or tungsten carbide, while the inner layer is made of a high-strength steel material.
The bimetallic screw barrel design provides several benefits, including increased resistance to wear, corrosion, and high temperatures. Additionally, the bimetallic barrel design is more cost-effective than a single material barrel because only the wear-resistant outer layer needs to be replaced when it wears out.
Benefits of bimetallic screw barrels
Wear resistance
The primary benefit of bimetallic screw barrels is their wear resistance. The outer layer is typically made of a wear-resistant material, such as nitrided steel or tungsten carbide, which significantly reduces the wear and tear on the barrel during processing.
Corrosion resistance
Bimetallic screw barrels are also resistant to corrosion. This is important because the plastic resins used in processing can be highly corrosive and can damage the barrel. The inner layer is typically made of high-strength steel, which is resistant to corrosion.
High-temperature resistance
Bimetallic screw barrels can also withstand high temperatures. This is important because plastic processing involves high temperatures, which can cause wear and tear on the barrel. The outer layer of the barrel is typically made of a material that can withstand high temperatures, which improves the longevity of the barrel.
Cost-effectiveness
Bimetallic screw barrels are more cost-effective than single material barrels. This is because only the outer layer needs to be replaced when it wears out, which reduces maintenance costs and downtime.
Applications of bimetallic screw barrels
Bimetallic screw barrels are used in a wide range of plastic processing applications, including extrusion and injection molding. They are used to process a variety of materials, including polyethylene, polypropylene, and PVC, among others.
Extrusion
In extrusion, bimetallic screw barrels are used to melt and form plastic into a continuous profile. Extrusion is used to create products such as plastic pipes, tubing, and film.
Injection molding
In injection molding, bimetallic screw barrels are used to melt and inject plastic into a mold. Injection molding is used to create a variety of products, including plastic toys, automotive parts, and medical devices.
Maintenance of bimetallic screw barrels
To ensure the longevity of bimetallic screw barrels, it is important to perform regular maintenance. This includes cleaning the barrel after each use and inspecting it for signs of wear and tear. If the wear is significant, the outer layer should be replaced.
Bimetallic screw barrels are essential components in plastic processing industries. They provide several benefits, including wear and corrosion resistance, high-temperature resistance, and cost-effectiveness. Bimetallic screw barrels are used in extrusion and injection molding applications and require regular maintenance to ensure longevity. By understanding the basics of bimetallic screw barrels, you can ensure that your plastic processing equipment operates at peak performance.
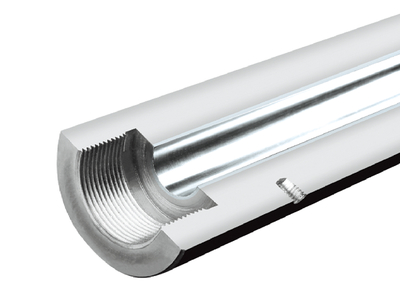
Zhoushan Intai Screw Manufacture Co.,Ltd. is a leading high-quality Bimetallic Screw Barrel manufacturer. By virtue of over 20 years of professional experience, INTAI has been growing at a steady pace and has been always committed to creating a world top provider of Bimetallic Screw Barrel. It owns a series of unique functions for R&D, design, production and aftersales which enable the products to be distinguished from others.
We only use first-class and check every production procedure to ensure precise production of every size. A final complete inspection will be performed before dispatch.