Chemical fiber extrusion plays a crucial role in the production of various synthetic fibers, such as polyester, nylon, and acrylic. The success of this manufacturing process heavily relies on the efficiency and quality of the equipment used, particularly the screw barrel. In this article, we will explore how choosing the perfect screw barrel can elevate your chemical fiber extrusion from mediocre to marvelous, revolutionizing your production capabilities and product quality.
Understanding the Importance of the Screw Barrel:
The Screw Barrel For Extrusion Of Chemical Fiber is the heart of the extrusion process, where the raw materials are melted, mixed, and pushed through the die to form the desired chemical fiber. Its design and functionality greatly influence the productivity, homogeneity, and consistency of the extruded fibers.
Factors to Consider When Choosing the Perfect Screw Barrel:
a. Material Compatibility: Different chemical fibers require specific material compositions and processing conditions. The screw barrel must be made from materials that can withstand the corrosive nature of the chemicals involved.
b. Design and Geometry: The screw barrel's design, including its length, diameter, and the number of zones, must be tailored to the specific requirements of the extrusion process. This ensures optimal mixing, melting, and homogenization of the raw materials.
c. Wear Resistance and Durability: Chemical fiber extrusion involves high temperatures and abrasive materials. Selecting a screw barrel with excellent wear resistance and durability will extend its lifespan and reduce maintenance costs.
d. Heat Transfer Efficiency: Efficient heat transfer is essential for achieving uniform melting and temperature control during extrusion. The screw barrel should have proper cooling mechanisms and thermal insulation to maintain the desired process parameters.
The Impact of the Perfect Screw Barrel:
a. Improved Product Quality: A well-designed screw barrel ensures homogeneous melting, mixing, and dispersion of additives, resulting in consistent fiber properties, reduced defects, and enhanced product quality.
b. Enhanced Productivity: The optimized screw barrel design enhances the extrusion process's productivity by minimizing downtime, reducing material waste, and allowing for higher production rates.
c. Energy Efficiency: The perfect screw barrel maximizes heat transfer efficiency, reducing energy consumption and lowering production costs.
d. Customizability: With the right screw barrel, you can easily adapt to changing market demands by adjusting the process parameters and optimizing the extrusion conditions.
The screw barrel is an unsung hero in chemical fiber extrusion, capable of transforming your production from mediocre to marvelous. By considering factors such as material compatibility, design, wear resistance, and heat transfer efficiency, you can select the perfect screw barrel that aligns with your extrusion requirements. Investing in the right equipment not only improves product quality but also enhances productivity, energy efficiency, and customizability. Take the leap today and unlock the full potential of your chemical fiber extrusion process with the perfect screw barrel.
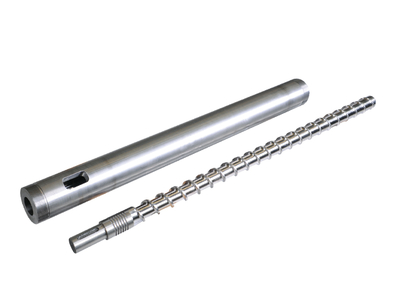
INTAI is devoted to the professional research and improvement of extrusion system. Its high-standard development caters for products demanded on the market. The rich experience and advanced technology for 20 years in barrel, screw, screen exchanger
and melt pump help you stand out among competitors. The screws for PET, PA6, PA66 and PP sliced melt spinning is made from LTM (low-temperature and mixed) elements with good plasticization. The adoption of professional processing technology produces high accuracy of manufacturing for screw and barrel and also sound linearity.
Field of application : PET, PA6, PA66, PP Chips , mainly used in low-speed, high-speed chemical fiber spinning;