The screw barrel is a crucial component of many industrial processes, particularly in plastic extrusion and injection molding. Over time, wear and tear can affect its performance, leading to reduced efficiency and quality issues. When faced with a worn or damaged screw barrel, manufacturers often face a dilemma: should they repair or replace it? This essay explores the benefits and considerations associated with repairing a screw barrel, shedding light on whether it is a worthwhile endeavor.
Advantages of Repairing a Screw Barrel:
1.Cost-effectiveness: Repairing a screw barrel can be a cost-effective solution compared to purchasing a new one. The cost of a replacement screw barrel can be significantly higher than the cost of repairs, especially for larger, specialized, or customized units. By opting for repair, manufacturers can save a considerable amount of money while restoring the functionality of the existing equipment.
2.Time-saving: Acquiring a new screw barrel involves a lead time, which can lead to production delays. Repairing the existing barrel eliminates the need to wait for a new unit to arrive, minimizing downtime and allowing production to resume more quickly. Time-sensitive industries can benefit greatly from this advantage, ensuring that production schedules remain on track.
3.Expertise and customization: Professional repair services offer specialized expertise in rejuvenating screw barrels. They possess the knowledge and experience to identify the root cause of performance issues and apply appropriate solutions. Additionally, repair facilities can often customize the repaired barrel to suit specific production requirements, further enhancing its performance and longevity.
Considerations for Repairing a Screw Barrel:
1.Extent of damage: The decision to repair a screw barrel depends on the severity and nature of the damage. Minor issues such as surface wear or damage to non-critical components are generally suitable for repair. However, extensive damage to essential parts or internal components may render repair uneconomical or ineffective, making replacement a more viable option.
2.Overall condition and age: Evaluating the overall condition and age of the screw barrel is essential in determining whether repair is worthwhile. If the barrel has undergone multiple repairs or if it is nearing the end of its expected lifespan, investing in a new one might be a better long-term solution. Balancing the cost of repair against the projected lifespan of the equipment is crucial for making an informed decision.
3.Technology advancements: Technological advancements in screw barrel design and materials may make newer models more efficient, durable, and compatible with evolving production needs. In such cases, replacing an outdated screw barrel with a technologically superior one might yield better long-term results, enhancing productivity and product quality.
Repairing a screw barrel offers several advantages, including cost-effectiveness, time savings, and the expertise of repair services. However, the decision to repair or replace should consider factors such as the extent of damage, overall condition, age, and technological advancements in the industry. By carefully evaluating these considerations, manufacturers can determine whether repairing a screw barrel is a worthwhile investment or if replacement is a more suitable option to ensure optimal production efficiency and quality.
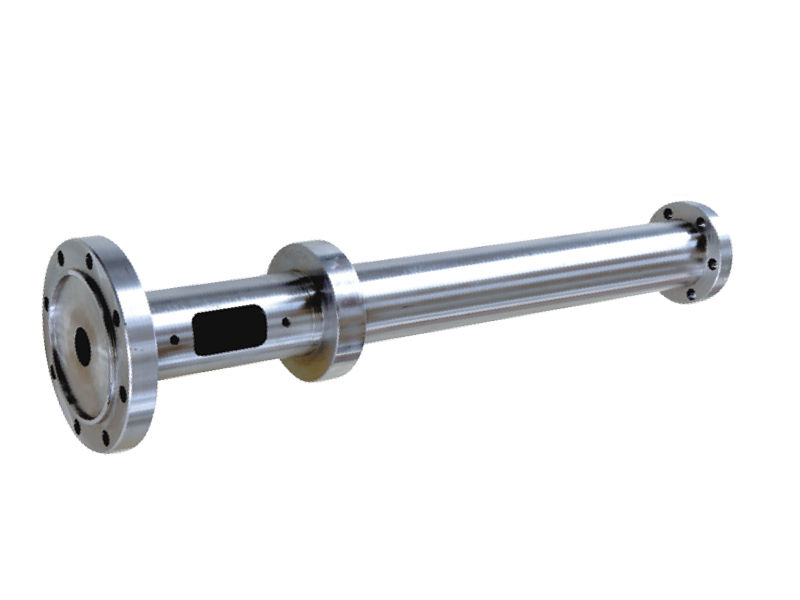
1.The broken screw should be repaired according to the actual diameter of the barrel. A new screw should be manufactured based on the designed outer diameter tolerance according to the normal clearance with the barrel.
2. The thread surface of the worn screw with shrinking diameter should be hot sprayed and painted with abrasion-resistant alloy after treatment, and then be ground to designed dimension. This repair is generally finished in a rofessional spray painting factory, and usually costs less.
3. The thread of a worn screw should be bead welded with abrasion- resistant alloy. It should be bead welded for 1-2mm thick according to the degree of wear and then be grounded to designed dimension. The abrasion-resistant alloy is made of materials like C, Cr, Vi, Co, W and B, which can improve the screw's resistance to wear and corrosion. Generally, this repair will cost much in a professional bead welding factory. Thus it is usually not adopted unless otherwise specified.