In the world of injection molding, the screw barrel plays a crucial role in the success of the entire process. It acts as the heart of the injection molding machine, responsible for melting and homogenizing the plastic material before it is injected into the mold. With the right knowledge and techniques, you can unleash the true potential of the screw barrel and enhance your injection molding process. In this article, we will explore key strategies and tips to optimize the performance of your screw barrel, resulting in improved efficiency, quality, and overall productivity.
Understanding the Screw Barrel
To enhance your injection molding process, it is essential to have a solid understanding of the screw barrel's functionality and components. We will delve into the anatomy of a screw barrel, including the screw design, barrel materials, and the critical role of heating and cooling systems.
Selecting the Right Screw Barrel
Choosing the appropriate screw barrel for your injection molding needs is paramount. We will discuss the various factors to consider when selecting a screw barrel, such as material compatibility, geometry, length-to-diameter ratio, and the significance of specialized coatings or surface treatments.
Optimizing Screw Barrel Design
The design of the screw barrel can significantly impact the performance of the injection molding process. This section will focus on key design considerations, including the flight depth and pitch, compression ratio, mixing elements, and the benefits of incorporating barrier sections or mixing pins.
Temperature Control and Heating Systems
Accurate temperature control is crucial to achieve consistent and high-quality results in injection molding. We will explore the importance of precise temperature regulation and discuss different heating system options, such as band heaters, cartridge heaters, and ceramic heaters, to ensure optimal melt temperature throughout the process.
Screw Barrel Maintenance and Cleaning
Regular maintenance and cleaning of the screw barrel are essential for its longevity and optimal performance. We will provide guidelines on proper maintenance routines, cleaning techniques, and the significance of screw and barrel alignment, as well as addressing common issues like wear, corrosion, and contamination.
Troubleshooting and Problem Solving
Injection molding processes can encounter challenges that affect the performance of the screw barrel. We will identify common issues such as screw slippage, melt fracture, screw wear, and how to troubleshoot and solve these problems effectively, minimizing downtime and maximizing productivity.
Innovative Screw Barrel Technologies
Lastly, we will explore the latest advancements in screw barrel technologies, such as barrier screws, screw and barrel coatings, and bi-metallic barrels. We will discuss their benefits and potential impact on enhancing the injection molding process, including improved mixing, reduced shear heat, and increased wear resistance.
By unleashing the full potential of your screw barrel, you can significantly enhance your injection molding process, achieving higher efficiency, superior product quality, and increased productivity. Understanding the screw barrel's functionality, selecting the right design, implementing precise temperature control, and performing regular maintenance are key steps towards achieving these goals. Furthermore, staying updated on the latest technological advancements can provide additional opportunities to optimize your injection molding process and stay ahead in a competitive industry.
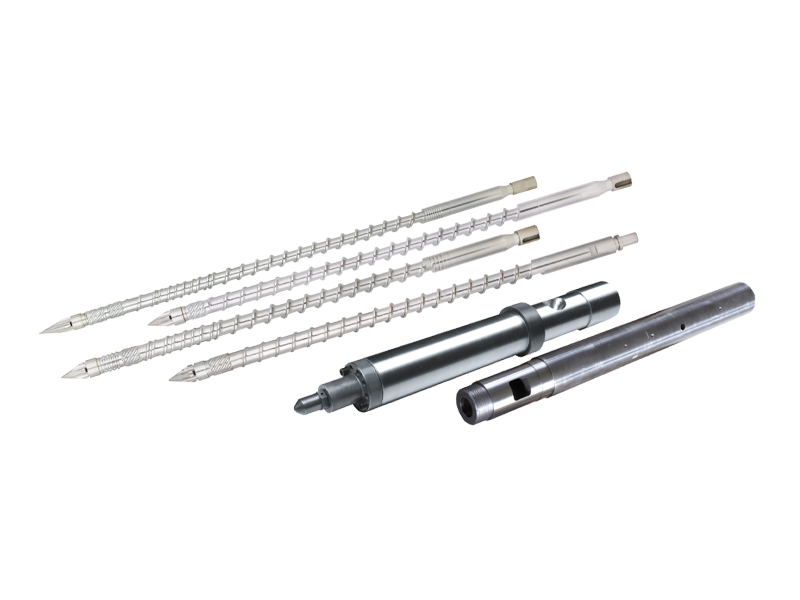
Screw Barrel For Injection Molding
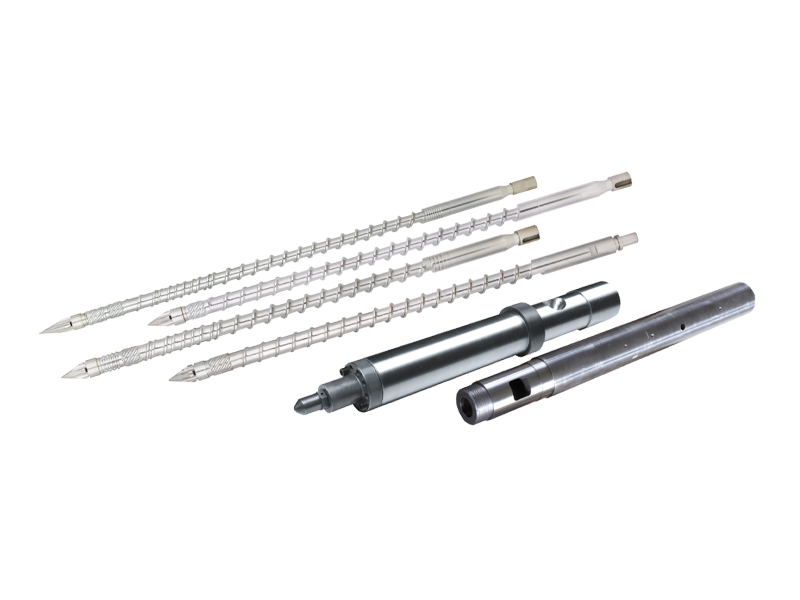
Screw Barrel For Injection Molding