The extrusion process is a widely used manufacturing technique that involves melting and shaping materials into a specific form. It is used in a wide range of industries, including plastics, rubber, and food processing. However, one of the main challenges faced by manufacturers is ensuring that their extrusion process is efficient and consistent. One solution to this problem is the use of bimetallic screw barrels.
A bimetallic screw barrel is made up of two different metals, typically a hard-wearing alloy on the inside and a softer steel on the outside. The combination of these two metals provides several benefits that help to improve the extrusion process, including longer life span, improved wear resistance, and better heat distribution.
One of the primary advantages of bimetallic screw barrels is their longer life span. The hard-wearing alloy on the inside of the barrel is specifically designed to withstand the wear and tear that comes with the extrusion process. This means that the barrel can last much longer than a standard barrel, reducing downtime and increasing production efficiency.
Improved wear resistance is another significant benefit of bimetallic screw barrels. The hard-wearing alloy on the inside of the barrel is resistant to abrasion and corrosion, which means that it can withstand the harsh conditions of the extrusion process without suffering significant damage. This helps to ensure that the extrusion process is consistent, and the quality of the final product is high.
Better heat distribution is also an important benefit of bimetallic screw barrels. The hard-wearing alloy on the inside of the barrel is an excellent conductor of heat, which means that it can distribute heat more evenly throughout the barrel. This helps to ensure that the material being extruded is melted and shaped consistently, which improves the overall quality of the final product.
In addition to these benefits, bimetallic screw barrels are also highly customizable. Manufacturers can choose from a wide range of alloys and materials to create a screw barrel that is specifically designed for their needs. This means that they can tailor the barrel to the material being extruded, which helps to improve the efficiency and consistency of the extrusion process.
In conclusion, bimetallic screw barrels are an excellent solution for manufacturers looking to improve the efficiency and consistency of their extrusion process. The combination of a hard-wearing alloy on the inside and a softer steel on the outside provides several benefits, including longer life span, improved wear resistance, and better heat distribution. Manufacturers can also customize their bimetallic screw barrels to meet their specific needs, ensuring that they get the most out of their extrusion process. With these benefits, it's easy to see why bimetallic screw barrels are the secret to longer-lasting extrusion.
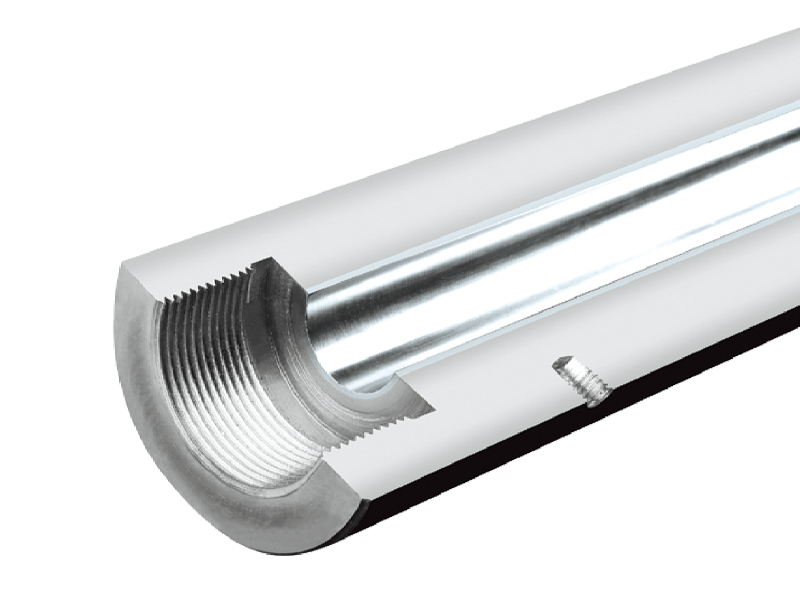
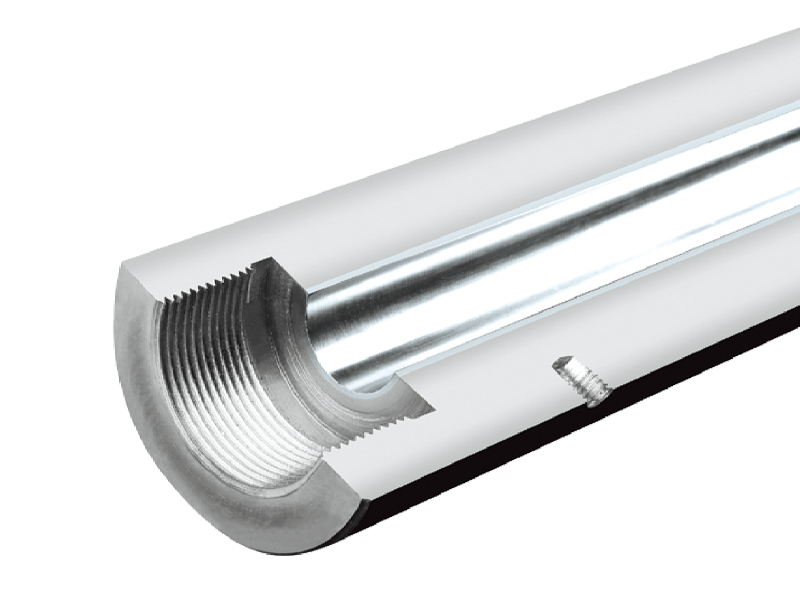
Application: all kinds of vertical and horizontal injection machines, extrusionmachines, injection machine, bakelite machine, rubber tube, blownfilm machine, etc.
Processing range: Dual alloy screw: diameter: Φ15mm -Φ360mm;Effective length: 10000mm
Dual alloy material tube: inner diameter 14mm -Φ200mm;Effective length: 6000mmSkin membrane density: 98-99.8%Hardness: Hv1100-1400℃Sticky strength: more than 10000Psi
Bimetallic barrel material: 38CrMoAlA、40Cr、42CrMo
Bimetallic screw material: 38CrMoAlA、31CrMoV9(foreign)
Screw / Barrel alloy powder (iron / nickel base):
GK - A: special-purpose alloy
GK - B: high wear resistance, high corrosion resistance, good
toughness, good crack resistance
GK - C: high wear resistance, high corrosion resistance
GK - D: high wear resistance
Field of application:suitable for LCP, PA + GF, PET + GF, PBT + GF, PC + GF all kinds of plasticadditives such as glass fiber, fire-proof agent, carbon powder and PPA, PPO,LCP, magnetic powder, special engineering plastics, such as PC.